Demand forecasting is modular and easy to configure. You can
turn the functionality on and off by changing the configuration key at Trade > Inventory forecast > Demand forecasting.
Demand forecast
variant conversion limitation
Unit of measure (UOM) per variant conversion is not
fully supported when generating demand forecast if inventory UOM is different
than the demand forecast UOM.
Generating forecast (Inventory UOM > Demand
forecast UOM) uses product UOM conversion. When loading historical data for
the demand forecast generation, the product level UOM conversion will be always
used when converting from inventory UOM to the demand forecast UOM, even if
there are conversions defined on the variant level.
Item allocation keys
Item
allocation keys establish groups of items. A demand forecast is calculated for
an item and its dimensions only if the item is part of an item allocation
key.
An item and its dimensions must be part of only one
item allocation key if the item allocation key is used during forecast
creation.
To create item allocation keys and add a
stock keeping unit (SKU) to them, follow these steps.
1. Go to Master
planning > Setup > Demand forecasting > Item allocation keys.
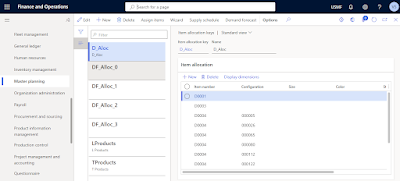
2. Either select an
item allocation key in the list pane, or select New on the
Action Pane to create a new one. On the header for the new or selected key, set
the following fields:
·
Item allocation key – Enter a
unique name for the key.
·
Name – Enter a descriptive name for
the key.
3. Follow one of these
steps to add items to the selected item allocation key or remove item
On the Item allocation FastTab, use the New and Delete buttons on the toolbar to add or remove items as needed. For each row, select the item number, and then assign dimension values in the other columns as you require. Select Display dimensions on the toolbar to change the set of dimension columns that is shown in the grid. (The value in the Percent column is ignored when demand forecasts are generated.)
If you want to add a large number of items to the key, select Assign items on the Action Pane to open a page where you can find and assign multiple items to the selected key.
Set up Demand forecasting parameters
Use
the Demand forecasting parameters page
to set up several options that control how demand forecasting will work in your
system.
Open the Demand forecasting parameters page
To
set up demand forecasting parameters, go to Master
planning > Setup > Demand forecasting > Demand forecasting parameters.
Because demand forecasting runs cross-company, the setup is global. In other
words, it applies to all legal entities (companies).
General settings
Use
the General tab of
the Demand forecasting parameters page
to define general settings for demand forecasting.
Demand forecast unit
Demand
forecasting generates the forecast in quantities. Therefore, the unit of
measure that the quantity should be expressed in must be specified in the Demand forecast unit field. This
field defines the unit that will be used for all demand forecasts, regardless
of the usual inventory units for each product. By using a consistent forecast
unit, you help ensure that the aggregation and percentage distribution make
sense.
Transaction types
Use
the fields on the Transaction types FastTab
to select the transaction types that are used when the statistical baseline
forecast is generated.
Demand
forecasting can be used to forecast both dependent demand and independent
demand.
For example, if only the Sales
order option is set to Yes,
and all the items that are considered for demand forecasting are items that are
sold, the system calculates independent demand.
However, critical subcomponents can be added to item allocation
keys and included in demand forecasting. In this case, if the Production line option is set to Yes, a dependent forecast is calculated.
You
can override transaction types for one or more specific item allocation keys by
using the Item allocation keys tab.
That tab provides similar fields.
Override default forecast algorithm parameters globally
Default
forecast algorithm parameters and values are assigned on the Demand forecasting parameters page (Master Planning > Setup > Demand forecasting >
Demand forecasting parameters).
However, you can override them
globally by using the Forecast algorithm parameters FastTab
on the General tab of
the Demand forecasting parameters page.
(You can also override them for specific allocation keys by using the Item allocation keys tab on the Demand forecasting parameters page.)
Use
the Add and Remove buttons on the toolbar to
establish the required collection of parameter overrides.
For each parameter in
the list, select a value in the Name field,
and then enter an appropriate value in the Value field.
All parameters that aren't listed here will take their values from the settings
on the Demand forecasting parameters page.
Set forecast dimensions
A
forecast dimension indicates the level of detail that the forecast is defined
for. Company, site, and item allocation key are required forecast dimensions.
You can also generate forecasts at the warehouse, inventory status, customer
group, customer account, country/region, state, and/or item level, and at all
item dimension levels. Use the Forecast
dimensions tab on the Demand
forecasting parameters page to select the set of forecast
dimensions that is used when the demand forecast is generated.
At
any time, you can add forecast dimensions to the list of dimensions that are
used for demand forecasting. You can also remove forecast dimensions from the
list. However, manual adjustments are lost if you add or remove a forecast
dimension.
Generate a statistical baseline forecast
When you create a baseline forecast, you must first specify the
parameters and filters that are used in the calculation.
For example, you can create a baseline forecast that estimates
demand based on transaction data from the past year for a specific company, for
the coming month, and for a selected group of items.
To
generate a demand forecast, go to Master
planning > Forecasting > Demand forecasting > Generate statistical
baseline forecast.
The forecast bucket can be selected at forecast generation time.
The available values are: Day, Week, and Month.
The
number of buckets to generate a forecast for is set in the Forecast horizon field.
When the forecast strategy is set to Copy over historical demand, the end of
the historical horizon is ignored. The system copies the number of buckets
specified in the Forecast horizon field
to the forecast demand, starting from the date set in the From date field under Historical horizon. By copying
historical demand from a certain date forward, production planners can make the
plan for the next quarter in two ways:
·
By copying the demand from the same quarter last year.
·
By copying the demand from the previous quarter.
To
prevent confusion in the production plans, a certain number of forecast buckets
can be frozen. This number is set in the Freeze
time fence field.
On the Adjusted demand forecast page,
the cells for the frozen buckets are disabled, to give a visual indication that
those values should not be changed.
The
start date for the baseline demand forecast doesn’t have to be the current date
or a date in the future.
To set a different start date, use the Baseline forecast start date - From date field.
For example, in June, users can generate a forecast for the next year. Because
the forecast buckets between the end of historical demand and the start of the
baseline are missing, the predictions might not be accurate.
The Baseline forecast start date - From
date field has to be set to the beginning of a forecast bucket, for
example, in the United States, a Sunday if the forecasting bucket is the week.
The system automatically adjusts the Baseline forecast start date - From
date field to match the beginning of a forecast bucket.
The Baseline forecast start date - From
date field can be set to a date in in the past. In other words, it is
possible to generate a demand forecast in the past. This is useful, because it
lets users adjust the forecast service parameters so that the statistical
forecast generated in the past matches the actual historical demand. Users can
then continue using these parameter settings to generate a statistical baseline
forecast for the future.
Manual adjustments made in previous demand
forecasting iterations can be automatically applied to the new baseline
forecast if the Transfer manual adjustments to the demand forecast
check box is selected. If the check box is cleared, the manual adjustments are
not added to the baseline forecast – but they are not deleted. Manual
adjustments made to a forecast can be deleted only at forecast import time, by
clearing the Save the manual adjustments made to the baseline demand
forecast check box. Manual adjustments are saved at authorization
time. Therefore, if a user makes manual adjustments to the forecast, but
doesn’t authorize the forecast back to Supply Chain Management, the changes are
lost. For more information about manual adjustments and how they work,
A demand forecast generation can have a name and
comments to help users identify the forecast that has been generated. These
values are visible in forecast generation history on the Statistical
baseline forecast generation history page.
The intercompany planning group, item allocation
keys, and other filters can be applied at forecast generation time. These can
be used to improve performance or to split the data into manageable chunks.
However, note that a demand forecast is not generated for the members of any
item allocation key that is not associated with an intercompany planning group,
even if the item allocation key is selected in the query.